

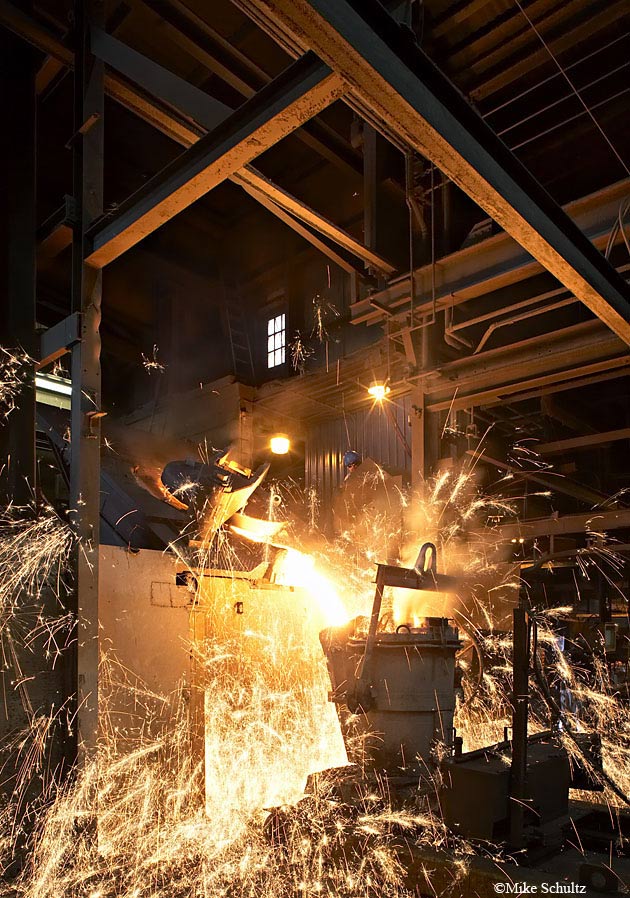
Avoid pattern wear and damage or lost patterns by storing and producing your design in 3D data. When a production run is of a limited quantity or a functional prototype is needed for testing, the best option is to skip pattern making altogether, saving time and money. Pattern making is always time consuming and generates significant additional tooling costs. What’s more, with our ExOne 3D printers we can do undercuts and cores that we would not be able to create with traditional foundry practices Using MAGMASOFT® solidification modeling, our engineering team tailors vents and risers to the part while running flow and solidification analysis to confirm the pour capabilities in advance to ensure quality castings. By concentrating our sandcasting capabilities under one roof, we can iterate designs quickly based on casting results and can communicate with customers and provide feedback to support their needs for unique runner and riser designs or other difficult requirements. Heat treatment capabilities located directly at our foundry also ensures our customers receive quick turnarounds.ĭelivering prototypes in less than one week is a gamechanger for metalcasting, opening the door to quicker product development and new freedom of design. electric induction furnace, allow us to do select melts for low-volume jobs without having to wait to fill a large furnace while also supporting poured castings as large as 1,700 lbs. The four furnaces at our facility, ranging from 300 lbs. Using additive manufacturing technology, we are able to produce sand molds and cores directly from digital CAD data that can go from print file to cast product within 5 days.
/zac89375_DH.jpg)
Typically, conventional manufacturing processes take about 40 days to produce a finished cast prototype, with the bulk of that time needed to build a pattern. Embracing the digital metalcasting workflow, Kimura has significantly reduced lead times for customer jobs.
